Uma pesquisa elaborada pela CNI – Confederação Nacional da Indústria, revelou que já em 2021, 86% das grandes empresas brasileiras utilizavam tecnologias digitais, capazes de aumentar a sua competitividade. Tupy e WEG, Associadas ABIFA, estão entre elas, conforme editorial da própria CNI: “Saiba como empresas brasileiras investem na transformação digital para aumentar a produtividade”, publicado no Portal da Indústria.
Abaixo reproduzimos os cases de ambas, para mostrar que a digitalização está ao alcance de todos. Embora se trate de duas multinacionais, as suas histórias rumo à digitalização começaram pequenas, com foco no básico, na coleta de dados para gerar informação; essa sim relevante. Ambas se valem da palavra simplicidade para definir o início de suas jornadas. Sim, é possível.
A digitalização não é exclusividade para as grandes. Ela é imprescindível para todas.
O caso Tupy
Para a empresa, a transformação digital é sobre tecnologia e pessoas. Com 20 mil colaboradores em seis plantas, a multinacional, com sede no Sul país, estruturou um time de transformação digital com 100% das pessoas que já trabalhavam na empresa.
Daniel Moraes, diretor de tecnologia e inovação, conta que o time de transformação da Tupy conta com profissionais das áreas de TI, automação, operação e colaboradores que trabalham na fábrica. “Assim, quando uma ferramenta digital é desenvolvida, já se sabe como conectar com o operador e com o supervisor, por exemplo. Isso ajudou a superar barreiras”.
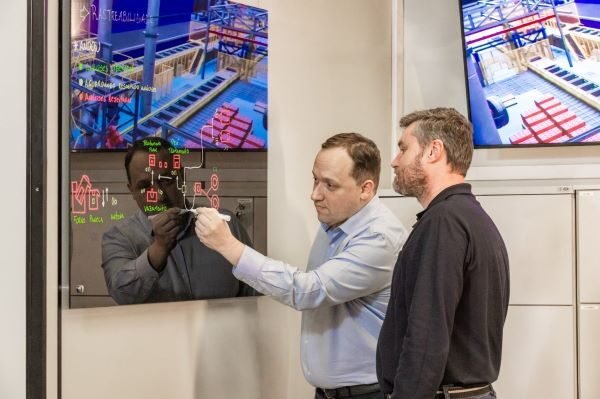
A jornada de transformação digital na Tupy se intensificou nos últimos cinco anos, quando foi criado um comitê de Indústria 4.0, com duração de um ano. A empresa convidou clientes de várias áreas e definiu pilares de transformação digital.
“Identificamos oito áreas de enfoque para gerar valor. Por exemplo, operações e equipamentos, até porque no Brasil temos muito retrofit”.
Outros pilares identificados foram: Gestão de ativos, manutenção, parte administrativa, clientes, desenvolvimento de pessoas, que envolve conhecimento, treinamento e formação, além de ESG e liderança de capital aberto.
De acordo com Moraes, esses pilares são construídos por tecnologia: Redes, conectividade e capacidade de coletar dados. Ou seja, “Internet das coisas industriais”. As conexões de campo foram revistas e agora as máquinas se conectam.
Com essa reestruturação para a jornada de transformação digital, atualmente, os processos industriais da Tupy contam com uma diversidade de tecnologias, como reconhecimento virtual de imagens.
Para mergulhar na transformação digital, Moraes afirma que há dois caminhos. Um oferece uma adoção de tecnologias com ações bem focadas e resultados de curto prazo. O outro, que foi a escolha da Tupy, é gradual.
“O primeiro caminho é mais limitado porque fica dentro do processo, da máquina. O outro consiste em fazer de forma mais estruturante, ou seja, pegar toda a fábrica, a infraestrutura básica de comunicação, conectar todas as máquinas adequando-as de forma estruturada e começar a gerar dados que são guardados em bancos de dados. Tendo essa conexão, tem-se uma estrada”.
Ainda segundo Moraes, o melhor caminho para as empresas se transformarem digitalmente é o da simplicidade. “Simplifique o tema. Tire a pressão de que sua empresa só será digital se for Indústria 4.0. A tecnologia não é um fim, é um meio, e ela tem que estar a serviço da empresa. O ideal é ir aos poucos, coletando dados. Além disso, encontrar parceiros. Os grandes saltos tecnológicos que tivemos foram fruto de parcerias com universidades, centros de pesquisa e ICTs”.
O caso WEG
Para a multinacional, também localizada na Região Sul do país, a “evolução digital” se intensificou nos últimos quatro anos. Nas palavras de Carlos José Bastos Grillo, diretor-superintendente de digital e sistemas da WEG, “melhorias se fazem por meio de evolução. A gente nunca se transformou digitalmente, fomos evoluindo: experimentando um robô, por exemplo, vendo como funciona”.
Para essa evolução digital, a empresa, que conta com 40 mil colaboradores, dos quais 4.700 são engenheiros, se debruçou sobre os conceitos da Indústria 4.0 e começou por introduzir produtos digitais nos produtos tradicionais que já fabricava, o que acelerou o processo na direção da digitalização.
Inicialmente, a empresa investiu principalmente em robôs autônomos, simulação de engenharia, integração de softwares e sistemas, big data, Internet das coisas, manufatura aditiva, realidade aumentada e cibersegurança.
“A adoção gradual dessas tecnologias costuma ter um retorno efetivo. O processo de digitalização às vezes passa a ideia de uma complexidade adicional, mas não é isso que queremos quando se busca simplicidade. Acredito que para as empresas menores, por exemplo, esse caminho possa até ser mais interessante”.
A aplicação dessas tecnologias, segundo ele, acontece de forma heterogênea, devido às diferenças entre os profissionais: “Alguns operadores podem até ficar reticentes por uma aversão à tecnologia, já outros podem se adaptar facilmente. A própria empresa vai encontrando seus caminhos. Mas uma coisa é certa: não dá para esperar. E vemos que algumas adiam o começo por acharem que precisam ter um sistema fantástico e grande. Então podem começar a encontrar desafios como pessoas, capacidade financeira para investir, tempo. A melhor forma, portanto, é começar pequeno, mas começar já”.
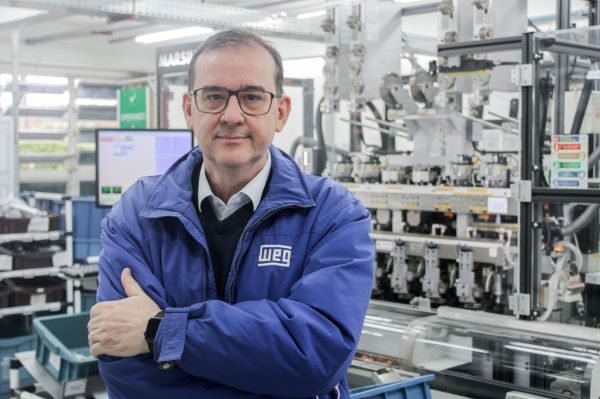
Segundo Grillo, o investimento da WEG em tecnologias habilitadoras da Indústria 4.0, que estão mais ligadas à engenharia de produto, como softwares de simulação e virtualização de produtos, têm custo maior. “Nesse caso, a empresa deve gastar em torno de 10% a 15% do seu custo de engenharia para se manter atualizada. No caso da engenharia, os custos são maiores, porém inevitáveis”.
Já na manufatura, o investimento em tecnologias digitais é menor. “Por exemplo, aplicar Internet das coisas para medir a vibração dos motores dos equipamentos. Esse custo equivale a 1% de investimento em uma operação industrial”.
Investir na digitalização, de acordo com o executivo, traz ganhos por proporcionar visibilidade aos processos industriais. “Na WEG, desenvolvemos produtos em prazos muito curtos, porque conseguimos fazer a simulação. Então, vemos a performance ainda no ambiente virtual. O que se monitora já se melhora. Se você não tem visibilidade sobre o que está acontecendo você não tem informação, apenas palpite”.
Outro exemplo é utilizar sensores nas máquinas, o que já aumenta a visibilidade. Em um processo de manutenção de equipamentos da fábrica de fios, por exemplo, a empresa reduziu 23% do custo de manutenção com a adoção de sensoriamento e softwares de diagnóstico, antecipado de falhas.